New VICON Cement Invented by SCI Technologies
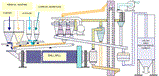
By K. Sobolev and C. Podmore, European University of Lefke
VICON or high-performance cement is an important breakthrough in cement manufacturing introduced by SCI Technologies. Now we can make high performance cements to order: from super-strong cements with rugged durability to low cost cements with up to 70% mineral additives. Using such a high volume of mineral additives (e.g. sand, limestone or various industrial by-products) has an important economic and ecological impact. VICON cement is stronger, cheaper and green.
High-Performance Concrete
As a result of the latest developments in concrete science the idea of high-performance concrete has been put forward and successfully applied worldwide in many construction projects. According to Dr. Forster, high-performance concrete is "a concrete made with appropriate materials combined according to a selected mix design and properly mixed, transported, placed, consolidated, and cured so that the resulting concrete will give excellent performance in the structure in which it will be exposed, and with the loads to which it will be subjected for its design life."
The key to the manufacture of high performance concrete is precise control. A variety of chemical admixtures and mineral additives must be used in exact doses: an error in mixing may have a dramatic transformation of the required properties of the high performance concrete. Further the compatibility of the admixtures must be tightly controlled. Precision is everything. The technology used in high-performance concrete plants is becoming like a sophisticated chemical or pharmaceutical process. Most regular concrete batching plants are inadequate to meet these requirements; they must be upgraded with equipment for precise control, dispatching, dosing and batch processing. Such upgrading means money. Why should a manufacturer bother with such extra investment?
The answer is that it pays to invest in highly efficient products occupying new market niches competing not only with conventional concrete, but rather with steel, natural stone, ceramic, and construction polymers.
High-Performance Cement
The new techniques help to keep costs to a minimum. At the same time a range of superior cement is available. The technology for producing cement has not remained static. It is under continuous development. Earlier, scientists developed a new cement which is ground with a calcined clay. As a result, a remarkable durability was obtained. However this technique produced cement of only regular strength. The manufacturing of special clinkers is another, but more expensive way of improving the performance of cement.
Now, by using a new admixture during the cement grinding process, a new high-tech product has been created by CSI Technologies: high-performance cement or VICON cement.
High-performance cement is versatile and promises to be a most suitable material for future construction projects. The central idea of this exciting product is the addition of a new reactive silica-based complex admixture during the grinding of the portland cement. Thus, in the case of VICON cement, the major process of passing raw materials through an extremely high-temperature furnace to produce cement clinker remains the same. The difference is that clinker is ground in a ball mill together with the admixture, mineral additives, and gypsum. The resulting cement is then available for distribution and use.
Importantly, in the production of high-performance cement the amount of clinker can be drastically reduced. The special qualities of the admixture produce a high-performance cement that is far superior to ordinary cement. Indeed, up to 70% of the cement clinker can be replaced by cheaper local additives: sand, limestone, natural pozzolanic or volcanic materials, fly ash, granulated blast furnace slag, broken ceramic and glass items. All these can be used as cheap indigenous mineral additives.
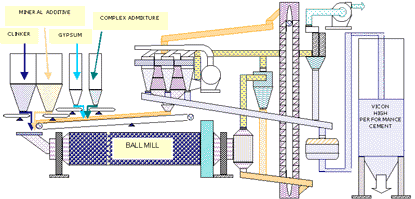
In the precision-blended high-performance cement, the use of granulated blast-furnace slag provides in addition to high strength a very high resistance to chemical attack and thermal resistance. Due to the consequent low permeability and more resistant chemical structure, the high-performance cement exceeds standard requirements for a sulfate-resistant cement.
Key Ingredients
The pre-made complex admixture requires reactive silica-based material. Different types of available clinker can be used in the proposed process, but best results were achieved with high C3S and mineralized clinkers. As a result, an optimized sample of high-performance cement achieved 28-day compressive strength up to 95 MPa (13,775 psi). The 1-day compressive strength of VICON cement was found to be of 44 MPa (6,380 psi), while 1 month is required for normal cement to reach this value. Similarly, compressive strength at 2, 3, 7 and 90 days were far higher than normal cements. Certainly this technique produces a cement in every way superior to the best types of cements available in the market. And at a competitive price.
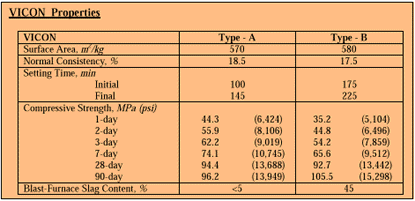
New Standard for a New Cement
Various standard procedures are in place to test and control the quality of cements. But these new high performance cements have a radically different set of characteristics from traditional cements. The ASTM C109 / C387 test procedure was found be the most appropriate. Obviously in measuring the properties of the new range of high-performance cements, a better testing procedure is required. The lack of standards appropriate to the breakthrough in high-performance is limiting the application of these new super-cements.
Global Warming & Eco-Considerations
The production of cement clinker is ecologically damaging and expensive. The raw materials are fed into kilns where flame temperature can rise as high as 2000 °C (even high comparing to normal steel which melts at 1600 °C). To simplify, we can say that 1 ton of normal cement produces 1 ton of carbon dioxide. Carbon dioxide is the principle gas contributing to the "greenhouse effect". While the exact effects of global warming are not known, there is sufficient concern to control the emission of carbon dioxide at the source. VICON cement uses about 50% less clinker than inferior cements and thus creates less ecological damage per ton of production.
Partly replacing the cement clinker, VICON cement incorporates sand, limestone, natural pozzolanic or volcanic materials, fly ash, granulated blast furnace slag, broken ceramic and glass items. Sand, limestone and natural pozzolanic materials may be locally available; they are cheap materials and their use is ecologically sound. Fly ash and granulated blast furnace slag are waste by-products of other industrial processes. By using these waste materials in cement production there is no need to transport this industrial waste to landfill sites which produces no economic gain. The recycling of broken glass and ceramic pieces is excellent ecological policy; again waste is used to an economic advantage. The need for landfill sites is also reduced.
VICON cement contributes to the reduction of carbon dioxide at source; it usefully and economically uses waste materials that otherwise would end up in landfill sites.
Cement Plant Expansion
Cement technology is highly capital-intensive with a slow return on investment. The manufacture of clinker is the most expensive stage in the production of cement. Therefore to expand an existing plant would require a proportionally high rate of investment. Instead of this heavy-handed approach to expansion, we can be smart and light-footed.
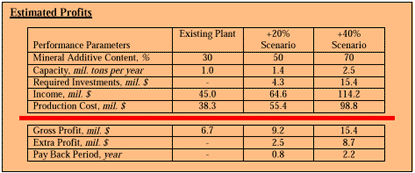
By altering the final grinding stage, we can save on expensive clinker and increase the production capacity by 30-50%. True, the installation of special control equipment would require extra investment. Demand for the complex admixture is also an additional cost. However, there would be immediate savings in the amount of cement clinker used. The increased capacity would certainly lift revenues.
Adoption of this new technique can only improve the bottom line. Failure to adopt will boost innovative trial companies.
Applications and advantages
VICON cement based concrete can be applied in high-rise buildings, pre-cast reinforced concrete structures, airport runways, bridges, marine or offshore structures, tunnels, parking desks, in shotcrete and repairing of structures, underwater concrete, and special floors.
The properties of VICON cement are quite remarkable, and there are considerable savings over existing construction procedures.
The most important economical benefits of VICON cement are:
- reduced cross sections of structures and consequent savings of concrete raw materials, structural steel and energy;
- reduced construction cost due to less total weight of structures and foundations, reduced total energy consumption, less formwork, less maintenance and equipment loading, and increased speed of erection;
- significantly increased lifetime of structures and reduced cost of repairs due to high durability.
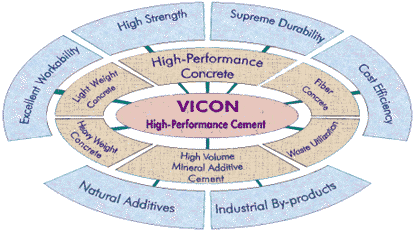
Furthermore, it could become the product of choice and specification in earthquake zones. The containment of nuclear and hazardous waste is also a promising area.
In summary, VICON cement is a cement with superior technical performance; it can be even cheaper than normal cement and has distinct ecological advantages. Neatly, VICON cement combines technological advance at a lower cost and is ecologically sweeter. Clearly a product for our future.
The application of this approach is not limited to materials with high strength and extreme durability, but it also can be utilized for the engineering of composite materials with special properties, such as low thermal expansion, electrical conductivity, light-reflection and many others. The high performance cement development team welcomes inquiries from potential partners for licensing, joint application and collaborative research.
SCI Con Technologies Inc., P.O. Box 394, Providenciales, Turks and Caicos Islands. Fax: +1-734-4486843; E-mail: cement@technologist.com; Web: http://sci-con.hypermart.net/SCI.html.