Selecting a Geomembrane Material
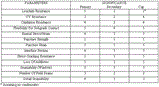
By Ian D. Peggs and Rick Thiel
As the number of available geomembrane materials Polyethelene (PE), Poly (vinyl chloride) (PVC), Polypropylene (PP), Chlorosulfonated Polyethylene (CSPE), Polyester (PET), Polyurethane (PUR), and their alloys increases and their range of applications widens, it is becoming more important that the proper selection of material, and even resin within one material type, be made. This cannot be done on an emotional basis, nor can it be done without a thorough knowledge of geomembrane performance. A technically based protocol is presented for selecting a material for each specific geomembrane application.
INTRODUCTION
The selection of a geomembrane material for landfill or liquid impoundment lining systems is often based on the prescriptions of federal, state or provincial regulations, or is based on the selection of the material that will most easily proceed through appropriate permitting processes. For the past several years high density polyethylene (HDPE) has enjoyed the position of geomembrane-of-choice and, in fact, "HDPE" has become almost synonymous with the word "geomembrane". However, in a few instances, such as for the containment of black liquor at pulp mills (Peggs et al, 1993), for the containment of nitric acid, and due to inadequate specification of resin properties, this has led to liner failures. In such instances alternative materials or resins would have provided better service, but the knowledge or appropriate mechanisms for the selection of the better materials or resins were not in place or were ignored.
The conditions under which geomembranes are used in lining systems are wide and varied. Geomembranes are required to provide service as the only, primary, or secondary liner of basal lining systems. The single, or primary geomembrane may be exposed to ultraviolet radiation or may be covered with soil, or it may be covered with a wide range of liquid chemicals. The primary geomembrane may be placed on an imported well-prepared soil layer, while a secondary geomembrane (never exposed to UV radiation except during installation) may be placed on a not-so-well-prepared (rough) natural subgrade. While the primary geomembrane may be constantly exposed to a chemical, the secondary geomembrane will not, or should not. If the primary geomembrane is exposed to UV radiation, it may also be exposed to wide variations in temperature (if liquid levels are varied), while the secondary geomembrane is not exposed to such wide changes in temperature. Thus, the service conditions experienced by primary and secondary geomembranes in the same basal liner may be quite different. There are similar, and more, differences required for the performance of geomembranes in landfill caps and floating covers, when compared to basal liners. Geomembranes in caps are subjected to differential settlement, permanent shear stresses, temperature variations, and perhaps vegetation root penetration that basal liners are not. They must be able to tolerate deformation far more readily than basal liners. Then there are different requirements for geomembranes used as canal liners, dam facings, vertical cut-off walls, fuel farm secondary containment, and portable storage for fuel and water.
There are many geomembrane materials available today--HDPE, Very Low Density Polyethylene (VLDPE), Linear Low Density Polyethylene (LLDPE), coextruded PEs, Poly (Vinyl chloride) (PVC), PVC alloys, Polypropylene (PP) (reinforced and unreinforced), Ethylene Propylene Diene Monomer (EPDM), Chlorosulfonated Polyethylene (CSPE), Bitumen (roll and spray products), Polysulfide (PS), Polyurethane (PUR) (roll and spray products), and Polyester (PET) - all with different performance characteristics. With this wide range it is inappropriate to assume that one material, even a regulatory prescribed one, will provide optimum, even adequate, performance. Even though many regulations and project specifications allow "proven equal" materials, the time and expense of proving equality are more than most facility owners are willing to incur. Thus, innovation and progress are stifled.
It is also necessary to understand that, just as there are many different geomembrane polymers, so there are many different HDPE resins with different performance characteristics. While all of these have very similar conventional strength, density, and deformation characteristics, their long term mechanical durabilities (stress rupture resistance) can vary by a factor of more than 1000. Thus, specifying "HDPE" alone is akin to requiring a bridge to be made simply out of "steel". One needs to be much more specific to obtain adequate or optimum performance from the installed facility.
Therefore, a technical approach based on polymer performance, geomechanics, constructibility, and other factors has been developed for the selection of the most appropriate geomembrane for each project specific application. Cost considerations then become a secondary, rather than the primary, reason for material selection. By using this approach the increasing number of geomembrane failures that are occurring might be reversed.
METHODOLOGY
The first step in the process is to identify all of the factors that are important for the successful performance of the geomembrane in the specific application in the specific project. As previously indicated, such factors will be different for primary and secondary liners, caps, and floating covers. Not only should basic material mechanical, physical, and chemical performance be considered, so also must installation conditions (temperature, wind), time between installation and designed service conditions, operational requirements, and maintenance requirements. Will the landfill liner/cover be left exposed before waste is placed? Will select waste be placed as the first layer? Will the liquid level be constant, or high in winter and low in summer, or vice versa? Will the owners want to make their own repairs? A complete listing should be made of all of these requirements.
The second step is to identify the relative significance of each of these parameters (requirements) on a scale of 1 to 5, with 5 being "most significant" and 1 being "of little (but still some) significance". Thus, UV resistance for an exposed leachate lagoon liner will receive a 5 rating, while for a secondary basal liner it will receive a 1, unless for some reason, during installation, sections of it were to be left exposed for some time, when it might receive a 2. Clearly, these ratings are somewhat subjective and are based on the experience of the rater.
Some of the factors and their relative significances in solid waste and liquid impoundment facilities are listed in Tables 1 and 2 respectively. Note that these should not be considered complete for any real facility since environmental conditions have not been defined. Also note the differences between primary and secondary geomembrane liner requirements.
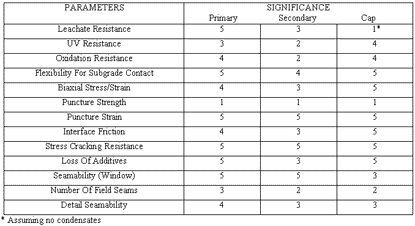
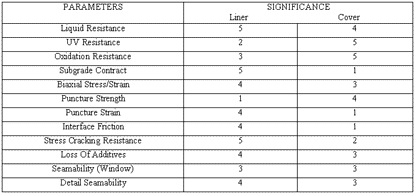
When all the significant parameters for each of the geomembrane components have been identified and rated, a number of candidate geomembrane materials (three to five) should be identified. Clearly, experience and judgment are usually required to develop the initial ‘short list' of candidate geomembranes. Cost should not be a factor at this stage of the selection process.
The performance of each of these candidate materials is then rated against each of the required parameters on a scale from 1 (poor) to 10 (excellent). A scale of 1 to 10 for only 3 or 5 materials allows emphasis to be given to extremely good or poor performance as required. The complete parameter/material rating system can be presented as shown in Table 3.
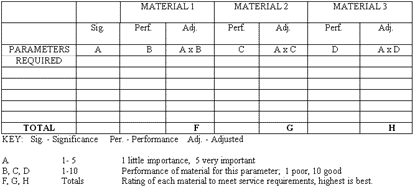
The significance and performance ratings (1 to 5 and 1 to 10) are multiplied to provide an adjusted rating for each parameter/material combination. All of the adjusted ratings for each material are then totaled to generate the final material rating. The highest value identifies the most technically appropriate material for that specific geomembrane application. Only now should factors such as cost be considered. And with this system, one generates a means of partially demonstrating "equivalency" of different materials.
As with any contrived rating system, experience and judgment are required in the final evaluation. There may be some technical parameters of overriding importance that are not adequately reflected in a subjective tabular rating. For example, achieving a minimum acceptable factor of safety for slope stability is often a fundamental design criteria that must be met with no compromise. In this case there is an absolute pass/fail criterion that candidate geomembranes must meet to qualify for further evaluation. Slope stability analyses on a specific project may reveal that only an aggressively textured geomembrane will be able to satisfy the requirements, and that textured polyethylene geomembranes are the only material available that is manufactured with such surfaces. But then the significance of that factor on the stress rupture resistance may have to be given more weight as well. Thus, the tabular matrix would then shift its emphasis from a range of fundamental polymer types, to a range of available polyethylene properties.
EXAMPLES
Four situations, all of which are contrived, and all of which are intentionally incomplete (so as not to become "prescriptions"), are described below.
CASE 1 - THE PRIMARY AND SECONDARY GEOMEMBRANES OF AN MSW LANDFILL. The secondary geomembrane will be placed on a coarse stony subgrade in a cold winter with the primary placed on a GCL in the following hot summer. The primary geomembrane will be covered immediately. Local regulators are aware of PP, and PVC, but are most comfortable with HDPE.
In this case the secondary geomembrane will have to tolerate subgrade scratching damage during installation and will have to tolerate puncture strains from the coarse subgrade. It will have to have some resistance to UV radiation since it may be exposed for up to 6 months. It will also have to have a low expansion coefficient so that excessive wrinkles are not formed at the high summer temperatures when it will be covered.
The evaluation presented in Table 4 indicates HDPE is most acceptable for the primary geomembrane, while PP is most suited for the secondary geomembrane.
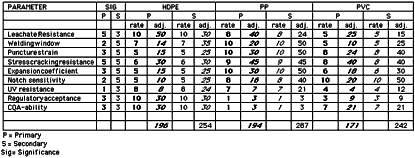
While it is an accepted fact that a composite liner constructed from a geomembrane and mineral layer/GCL produce the optimum lining system, similar recognition has not effectively been given to the benefits of using two different materials in double geomembrane lining systems, where the negative aspects of the primary geomembrane are complemented by the positive aspects of the secondary. Thus the chemical resistance and strength of an HDPE geomembrane can be complemented by the strain tolerance, low expansion coefficient, flexibility, and stress cracking resistance of a more flexible geomembrane. The secondary geomembrane does not require the same chemical resistance since it is not constantly exposed to the contained liquid, but it will conform better to the subgrade because of its flexibility (providing a better composite action than will HDPE). In cold environments compensation wrinkles in a flexible secondary geomembrane will not present a problem when placing an HDPE primary geomembrane, also with compensation wrinkles, on top of it, as might happen if the primary HDPE geomembrane were placed on top of a wrinkled secondary HDPE geomembrane. There is much to be said for having primary and secondary geomembranes made from different materials. (Note that the decision to use different materials for primary and secondary liners may also need to take into account the need to weld the primary and secondary liners together in the anchor trench to prevent water from entering the leak detection system. This is a site-specific issue that could be incorporated into the rating procedure.)
CASE 2 - THE EXPOSED PRIMARY GEOMEMBRANE IN A PULP MILL BLACK LIQUOR POND that will be installed in the summer in a location where winter temperatures can reach -40°C. The pond will mostly be empty except for three-week plant maintenance periods. "Detergents" will not be skimmed off the liquor. The black liquor enters the pond site at a temperature of 82°C.
Although efforts are made to reduce the temperature of the black liquor by cascading or spraying it into the pond , the liquid is still relatively warm. But is this necessary if exposed black liners regularly experience temperatures of 80°C in the summer sun? Chemical resistance to the liquor is of extreme importance as is the concern of thermal contraction of the geomembrane at low winter temperatures. Compensation wrinkles may need to be built-in in the summer installation.
Table 5 indicates PP and CSPE appear to be technically the most suitable materials.
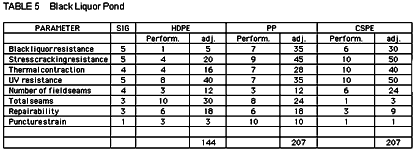
CASE 3 - A CO-DISPOSAL (MSW/CDD) LANDFILL CLOSURE CAP where temperatures vary somewhat but are never very high. Installation occurs in the summer. The waste is subject to differential settlement. There is an active landfill gas removal system incorporated in the lining system. The geomembrane is placed on a GCL on 3:1 slopes.
The cap will have to tolerate the strains of differential settlement, and the stresses induced by some temperature changes. Maximum temperatures are not so high that loss of plasticizers from PVC is of concern.
Table 6 indicates that PVC is technically the optimum geomembrane. However, slope stability analyses indicate that the interface friction between PVC and the underlying GCL is not adequate to meet the minimum required factor of safety of 1.5. In this case, consideration of a well-textured LLDPE is warranted if its interface shear strength is able to meet the requirements.
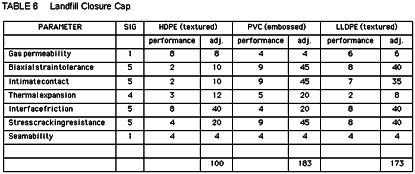
CASE 4 - AN UNDERGROUND CONCRETE RESERVOIR for storage of irrigation water for a golf course. There are many square concrete pillars supporting the roof. All corners between pillars and floor, and walls and floor, are right angles. There are cracks in the floor.
Table 7 indicates that a spray on polyurea liner is the optimum liner for this application.
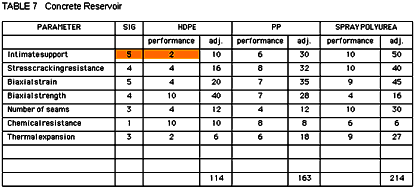
Clearly these examples have been contrived to generate different solutions and should not be considered complete, either in the parameters of significance, nor in the selection of candidate geomembrane materials, but they do provide examples of the types of thought processes and evaluations that are required for the successful selection and functioning of a geomembrane. There is not one geomembrane material that will be suited for all applications.
Even though this methodology may lead the specifier to an appropriate geomembrane material, care still needs to be taken in the details of the final specification. For example, when specifying HDPE, the stress rupture performance characteristics (stress cracking resistance) should be matched with the criticality of the specific lining installation.
Finally, it should be noted that there are many benefits to be gained from using different, but complementary, materials for the primary and secondary geomembranes of double lining systems.
CONCLUSIONS
A simple technically based procedure has been developed for the selection of the most appropriate geomembrane material for project specific applications. The procedure takes into account the operational and maintenance requirements of the facility as well as the mechanical, physical, and chemical performance characteristics of the material.
The procedure also provides information for a basic assessment of technical equivalency of different materials.
As with all engineering construction materials, experience, judgment, and a knowledge of the performance of such materials in such applications is essential in order to mobilize the optimum performance of the finished product.
REFERENCES
Peggs, I.D., Dewijn, T., and Lewis, D.R. (1993), "Geomembranes for the Containment of Pulp Mill Hot Black Liquors: Problems and Remediation", Proceedings of Geosynthetics ‘93, IFAI, St. Paul, MN.