The Primary Impact Crusher: Made for Concrete Recycling
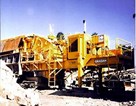
Aggregates producers and recyclers of concrete and asphalt rubble and C&D (construction and demolition) debris basically use two types of comminution devices: compression crushers and primary impact crushers. The primary impact crusher is far more productive for recycling as well as many aggregate-crushing operations.
Compression crushers are of three varieties--all being designed to handle aggregates and each having its limitations for recycling applications.
Jaws normally are used as primary crushers, handling incoming, previously uncrushed materials. Because of their small reduction ratio, jaws normally find use in combination with cone and roll crushers that further reduce the size of materials coming from the primary and secondary crusher. The jaw/cone (primary/secondary) combination is most common.
Impact crushers shatter materials by striking them with blow bars mounted on a horizontal rotor. Rotor speed can be varied according to the type of application and materials being crushed.
Prior to WWII, impact crushers mainly found use as secondary aggregate crushers. After the war certain horizontal-shaft impact crushers were designed by Hazemag specifically as primary crushers to process rubble in bombed out cities. It has major advantages over any jaw, jaw/cone, or jaw/cone/roll combination for recycling operations.
The recycling impact crusher is much faster and has a larger reduction ratio than a jaw crusher. Thus, it is more efficient and usually does not require a secondary crusher. Generally, a primary impact crusher costs more than a jaw crusher but less than a jaw/cone system, and thus can save money in its purchase as well as in more efficient production.
A jaw crusher bites up large pieces of material, such as concrete slabs and lengths of curbstone, slowly, piece by piece, and often leaves steel mesh and rebar still embedded in the concrete. The recycling impact crusher shatters concrete instantly, leaving steel clean enough to be segregated by an electromagnetic separator on the discharge conveyor for sale to a metals recycler.
Nearly all recycling impactor crushers sold today are road portable—to go where needed and work on site. They range in size from the small, self-contained mini-crusher types designed for use in cramped urban areas to large plants capable of crushing rubble at up to 600 or more tons per hour.
Often recycling impact-crusher plants are set up at road or building demolition and construction sites to crush rubble on the spot for possible immediate use as roadbed, fill, or sub-base for pipelines, buildings, and parking lots. Such availability reduces or eliminates the need to purchase aggregate and results in additional savings in time and hauling costs.

Many quarry operators use the recycling impact crusher instead of jaw crushers and jaw/cone combinations for crushing limestone with a low to normal silica content because of its efficiency and versatility. Some quarry operators also use road-portable impact-crusher plants to disintegrate recyclables, going from quarry to quarry to crush shot limestone as well as accumulations of concrete and asphalt rubble hauled in by local construction and demolition contractors.
Primary impact crushers also find application at landfills for crushing rubble and C&D debris. Materials such as drywall, asphalt shingles, wood, and dirt--often included in C&D debris--pose no problem for properly designed impact-crusher systems that include such attendant operations as picking stations, air classifiers, wood shredders and electromagnetic separators.
Impact crushers are available in primary and secondary varieties. The former's design is suitably substantial to withstand the rigors of continuous large-object breakup. Secondary crushers occasionally are unadvisedly substituted for primary crushers by enlarging their intakes. Each type crusher has its place and should be used accordingly.
Contact: Grasan, Don Schendel, 440 S. Illinois Ave., Mansfield, OH 44907-1809. Tel: 419-526-4440; Fax: 419-524-2176